Trailer Repairs and Checkups
Call before any trips, vacations or important events for a checkup.
Ten Most Common Trailer Repairs
The fleet administration of trailers and other properties is like traffic control at an airport. You have to. Have an eye for detail, and one of the most crucial points: is providing it in a timely manner. While modern. Technology assists a lot in improving the top quality of road transportation; it does not imply that it all goes. Automatically. Using trailers and trucks for roadway transport requires a great deal of the product. Heavy tons, high hills, or busted roadways can hurt your trailer more than you like.
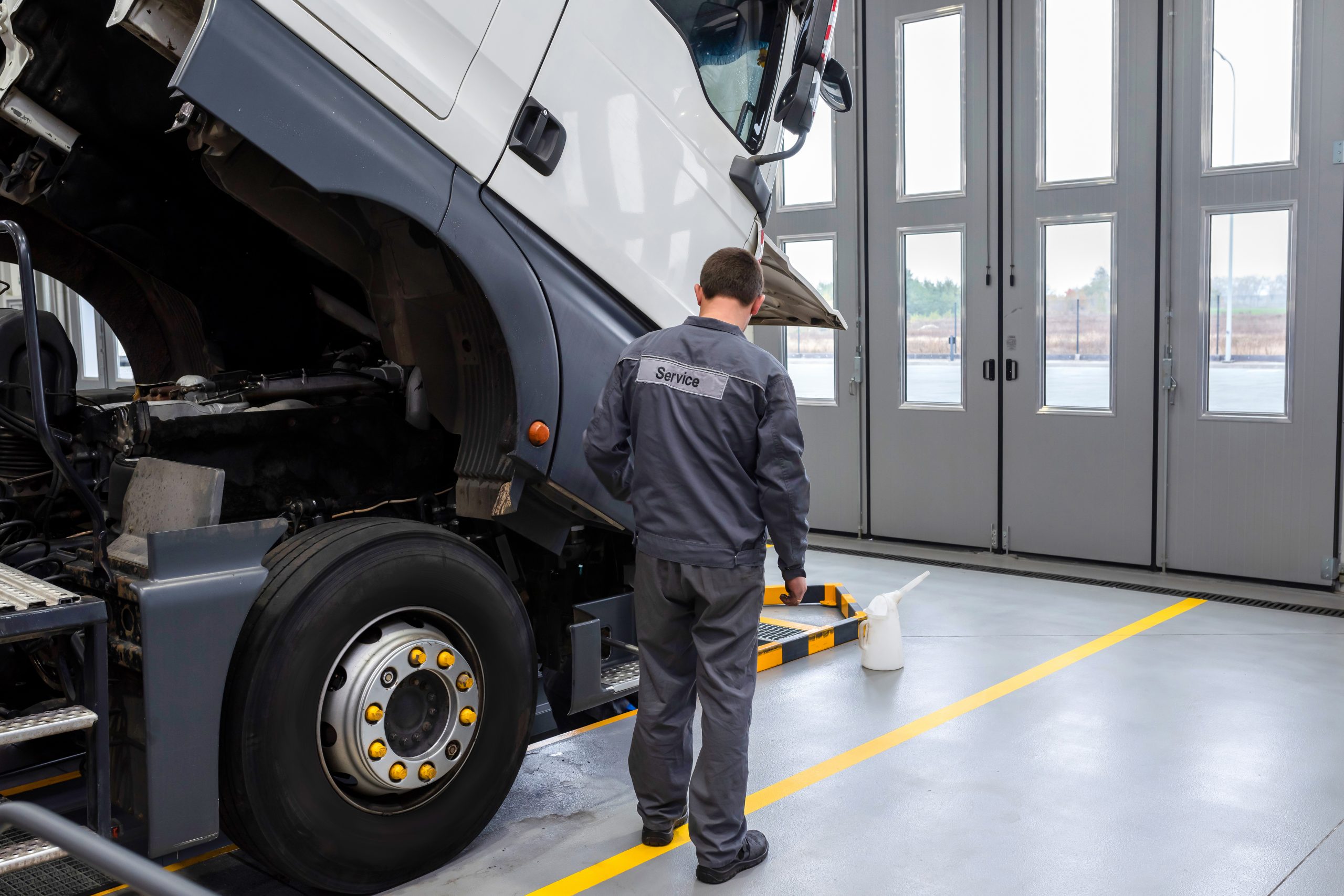
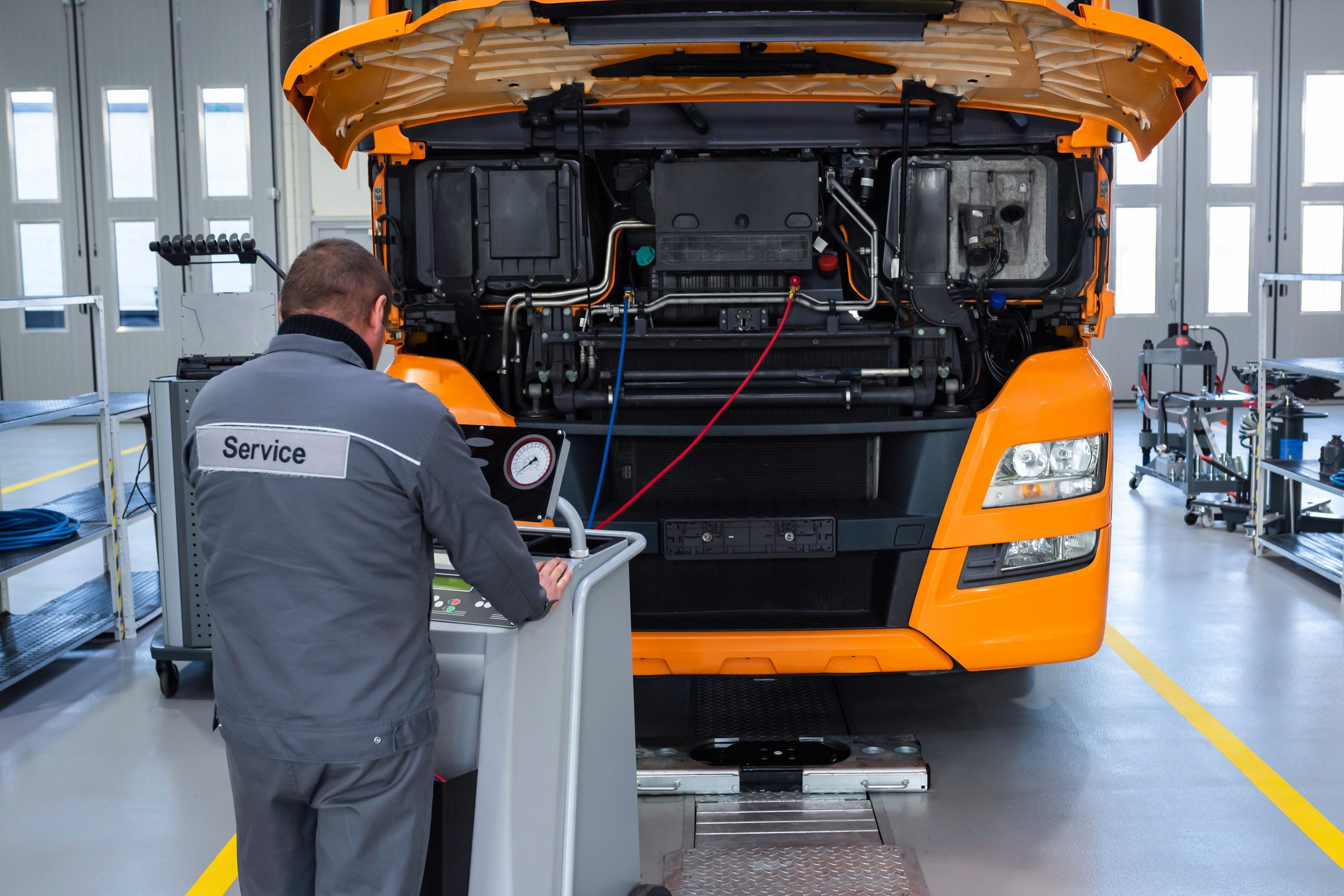
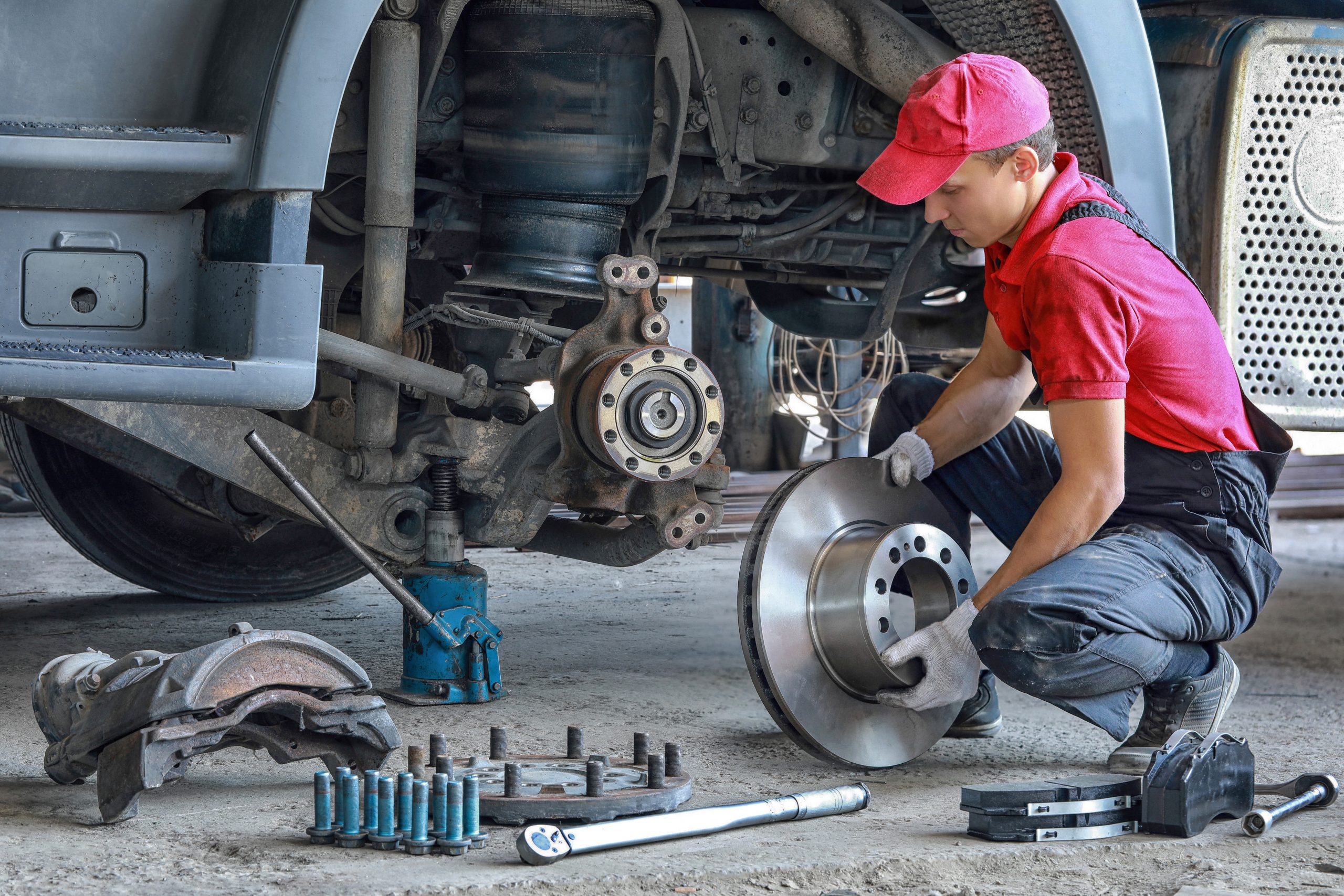
MAINTENANCE
The last point you desire is that your trailer is ‘decreasing’ due to the severe use.
Property. The enchanting word to stop this from occurring is MAINTENANCE. Some take Upkeep. As an irritating, costly affair, and they will fix things on their trailer when it’s essential. Others look at maintenance in a much more specialist method; they deal with every trailer as a part of the. Household fleet. A trailer needs love and attention and has to be looked after, both by the chauffeur and. By the fleet supervisors. With routinely arranged Upkeep, you can prevent a lot of troubles. And also. If you want to remain ahead of the competitors, you ensure that your firm will never be. A trailer incident impacted me. You can foresee technical problems with a trailer and also make. Sure that the repairs are done before the trailer is on the road, going from A to nowhere.
This effective tool is called Anticipating Upkeep.
PREDICTIVE MAINTENANCE
When you combine all trailer information with information concerning the gas mileage of a trailer, its age, and the. With regularly arranged maintenance, fleet managers can forecast the future of a trailer—this projection. It is to stay clear of possible malfunctions inside your trailer fleet—a brand-new step into maximizing yours. Service. With Predictive Upkeep, you also acquire optimal control of your trailer’s problem. Your future expenses. Whether you need a split-second, regular, preventative, or predictive trailer upkeep, TIP Trailer.
Solutions constantly examine a trailer thoroughly. We manage brakes, air system, air pressure, tires,
The electrical circuit, damage on the chassis, wall surfaces, ceiling, doors, locks, etc. The idea was technological. Experts in the idea workshops take care of your trailers as if they were their very own. As well as obviously, they. Have their stats about the Ten Many Common Trailer Repair Works. Use this to recognize what you can.
Anticipate the next time you make a stop at one of the suggested Trailer workshops in Europe.
- Repair body components such as bumpers, wing flaps, and bicyclist protection bumpers.
- Repair pneumatic aspects such as brake hand shutoffs, airline, etc.
- Fixing of rolling equipment and suspension: cushion suspension, suspension shutoff.
- Preparation & & pass the technical examination: precautionary check out, tailgate control.
- Repair services of electric tools such as lights, lights, sockets, and water-proof boxes.
- Repair work of liftgates: maintenance and also installment.
- Repair work as well as upkeep of the refrigerator group.
- Repair work of tires such as regrooving, retreading tires, or replacements.
- Fix brakes with EBS diagnostics, pad, or brake drum substitutes.
- Fixing of doors, rolling doors, and drape fixings or replacements.
The fleet administration of trailers and other properties is like traffic control at an airport. You have to. Have an eye for detail, and one of the most crucial points: is providing it in a timely manner. While modern. Technology assists a lot in improving the top quality of road transportation; it does not imply that it all goes. Automatically. Using trailers and trucks for roadway transport requires a great deal of the product. Heavy tons, high hills, or busted roadways can hurt your trailer more than you like.
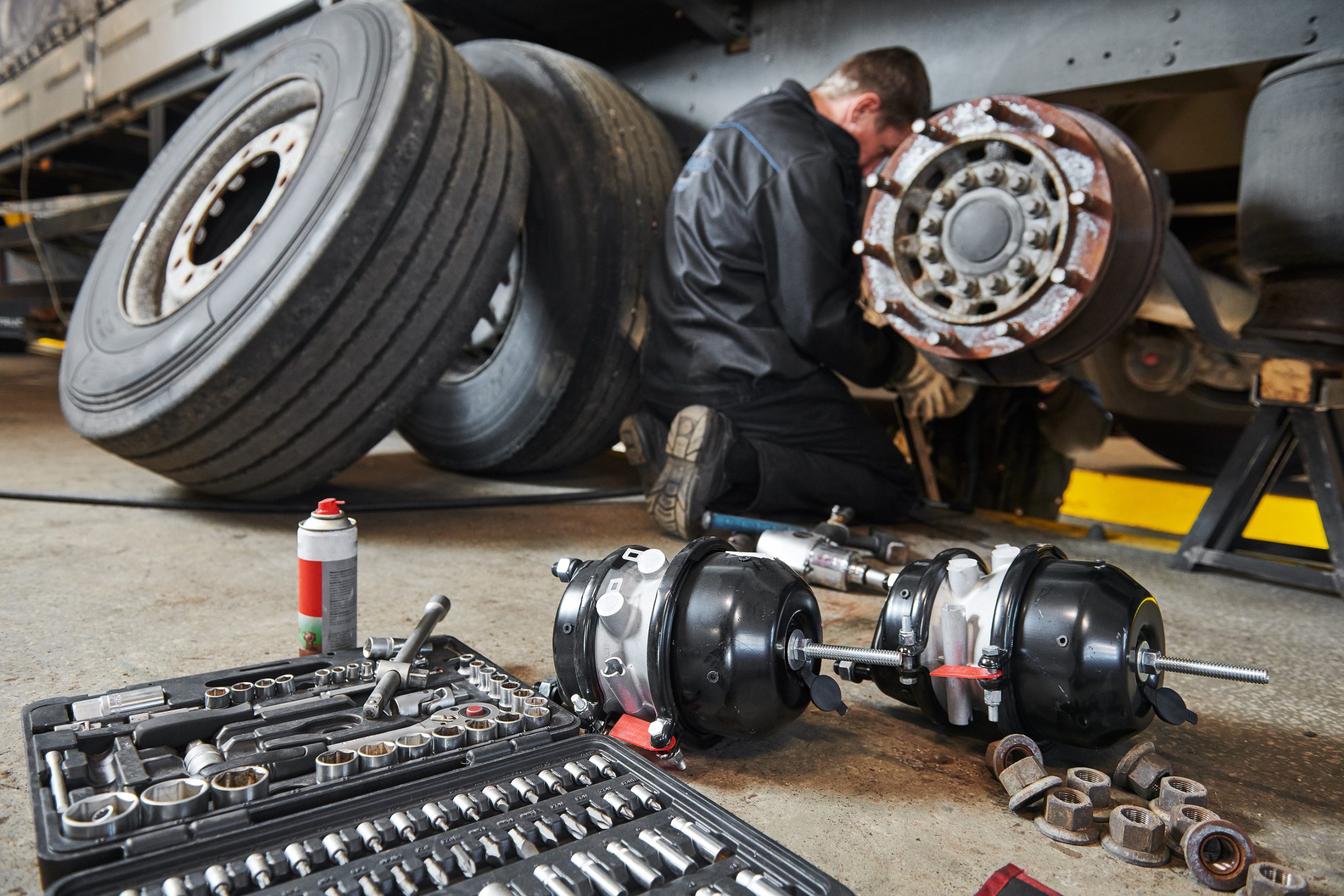
For more information about your trailer fleet maintenance and the power of our Mobile Road Assistance vans in Europe, contact us here.
Trailers, much like any other piece of equipment, ultimately break down. Nevertheless, they are put through quite an exercise every time they are made use of. Busted roads, high hillsides, and heavy lots take their toll. As well as, if not looked after, they will break down even quicker. Taking excellent care of your devices as well as looking for the most generally taking place damages or malfunctions can aid keep your trailer in good problem.
We put in the time to speak to a variety of people who transport trailers for a living and got some valuable outcomes. Let’s look at a handful of the most typical troubles with the cars we tow behind our automobiles.
PREDICTING THE FUTURE
Before we look at the most breakdowns or issues with trailers, let’s look at what we can do to head these problems off right from the start. The future of a trailer can be predicted by taking a close, hard look at its age, the mileage it has traveled, whether or not regularly scheduled maintenance has been completed, etc. But not everyone knows what to look for. You may consider having regularly scheduled maintenance done on your trailer by a professional at a qualified service center.
MAINTAIN YOUR TRAILER
A professional will look at locks, doors, ceilings, walls, chassis damage, electrical circuits, tires, air pressure, the air system, brakes, and more. (These items apply to specific trailers, but you get the idea.)
Specifically, if you use your trailer for a living, when it’s down, there is no money being available. Preventative upkeep, predictive upkeep, and regular maintenance all go hand-in-hand and are a vital part of owning a trailer. If that is, you always want it up and running as much as feasible. Like your car has regularly arranged maintenance needs, so does your trailer.
MORE COMMONLY NEEDED TRAILER REPAIRS
As suggested earlier, certain areas of trailers break down on a more frequent basis than do others. Again, some of these apply to specific types of trailers, but it’s an excellent place to start:
- The repair or replacement of doors – i.e., curtain repairs, rolling doors, etc.
- EBS diagnostics with the restoration of brakes – i.e., brake drum replacement, pad replacement, etc.
- Tire repair or replacement – i.e., retreading tires, regrooving, etc.
- Maintenance and repairs of the refrigerator group.
- Liftgate repairs – i.e., installation and maintenance.
- Electrical equipment replacement or repair – i.e., waterproof box, socket, lamp, lights, etc.
- Technical inspection (preparation and pass) – tailgate control, preventative visits, etc.
- Suspension and rolling gear repair or replacement – i.e., suspension valve, cushion suspension, etc.
- Pneumatic element repair or replacement – i.e., air hoses, brake hand valves, etc.
- Body component repair or replacement – i.e., cyclist protection bumpers, wing flaps, bumpers, etc
At RB Hitch, we handle a variety of trailer repair issues, and we are capable of running maintenance checks on them as well.
BONUS BELOW
Just Call with Questions. We are a mobile service so we are on the road all day long. Remember we come to you.
Call with any question: Robby Billings at 352-572-1090
TRAILER LIGHTS INSTALLATIONS AND REPAIR
How to Repair or Install Trailer Wiring

If you’re installing a trailer hitch on your car or truck, you’re going to need a plug for the trailer lights. Trailer wiring can be very, very frustrating. If you’ve ever found yourself in a Walmart parking lot, in the dark, in the rain, trying to fix your trailer wiring with flashlights you know how much fun it can be. If you’ve got bad wiring, now’s the time to run some new wires, not when you find yourself in a pinch. Whether it’s a new installation or a repair job, we can help you with your trailer lights, wiring, and installation.
Please note: this is a basic installation, and all jobs are a little different. If you’re installing a larger trailer with electric brakes, you’ll need a brake controller, which will involve some wiring to be done under the dash.
If you like to keep tabs on all of your trailer wiring functions like electric brakes, brake lights, turn signal flashers, and running lights you might consider buying a trailer plug tester. They make these testers for small and large wiring plugs and they really make troubleshooting your trailer wiring much easier!
You’re almost done! The only thing to do now is test your new wiring at the critical point — the trailer connector. Get your buddy to pitch in again, and go through the lights one by one, checking to be sure there is a signal at the trailer connector. If you get a light every time, you’re done! Now you can put your tail lights back.
If one of your circuits doesn’t seem to be working, go back and check the connection to be sure. If the connection seems good, check the fuse. Sometimes you can blow a fuse without even knowing it. Read more.
5TH WHEELER HITCH INSTALLATIONS
5th Wheel Hitch Installation How-To
How do you install a 5th wheel hitch? Installing a 5th wheel hitch involves removing the spare tire, measuring where bolt holes need to be drilled, drilling into the truck bed, assembling the 5th wheel hitch, measuring the trailer height, installing bolts and torqueing hardware.
In the following guide, we will go step-by-step through the process of 5th wheel hitch installation. Remember to follow the specific instructions for assembly when mounting your own 5th wheel hitch.
2. Position the front base rail
3. Mark the first drill location and drill a pilot hole
4. Check the pilot hole under the truck bed and drill the remaining holes
5. Enlarge the bolt holes
6. Bolt in the under-bed brackets
7. Bolt down the front 5th wheel rail
8. Measure the 5th wheel hitch height
9. Attach the 5th wheel legs
10. Position the rear 5th wheel rail
11. Drill holes for the rear base rail
12. Bolt down the rear base rail
13. Install any remaining bolts
14. Torque all hardware
15. Secure the 5th wheel hitch
Your content goes here. Edit or remove this text inline or in the module Content settings. You can also style every aspect of this content in the module Design settings and even apply custom CSS to this text in the module Advanced settings. Read more.
TRAILER HITCH INSTALLATIONS
How to Install a Trailer Hitch in 8 Step
Installing a trailer hitch is a relatively easy automotive job. A typical tow hitch installation may involve some of the following steps: removing the spare tire, lowering the exhaust, removing existing vehicle hardware, lifting the hitch into position and torqueing the hitch hardware to the correct values.In this guide, we”ll cover step by step how to install a hitch. We’ll also answer questions about cost, time, warranty and offer some pro tips.
We would like to thank Curt Manufacturing for helping with this list.
CURT hitches are especially easy to install because most are no-drill and require only a few simple tools. If you’d prefer to take your vehicle in for professional installation, CURT also has a complete network of dealers and installers.
TOWING TIP!
Before purchasing a hitch, look up the installation instruction sheet or installation video online for the hitch you are considering, and then decide if it is something you can handle on your own or if you will need to bring it to a professional installer.
Step 1: Read the instructions
The first step to installing a trailer hitch receiver is to read the instructions. Familiarizing yourself with the steps involved in the installation will give you confidence in your work and will help you determine if you’re up to the task.
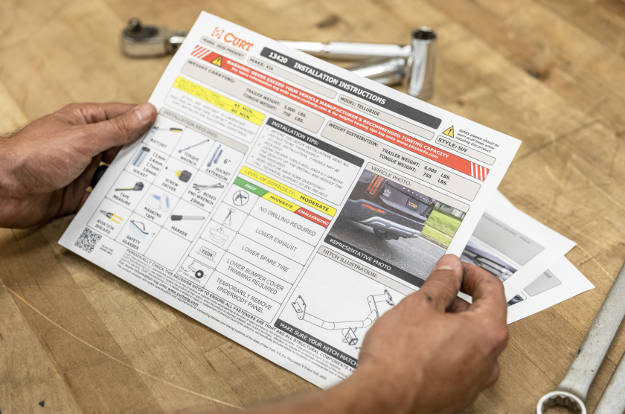
Step 2: Gather your tools
Before you begin, set aside the tools necessary for the tow hitch installation. These may be different depending on your specific hitch, but in general, a hitch installation only requires some basic tools found in the average do-it-yourselfer’s tool box.
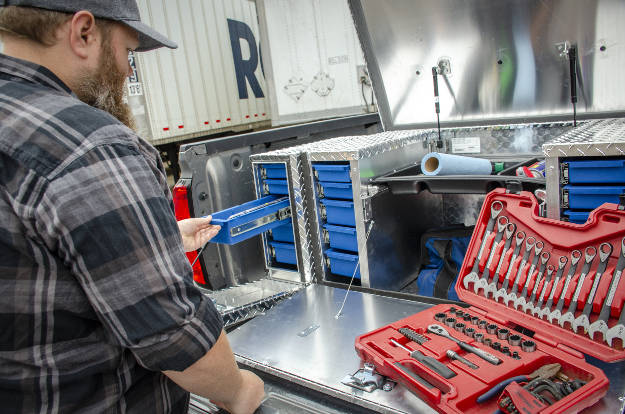
Step 3: Chock your wheels and jack up your vehicle
Next, you will need to place wheel chocks on your front wheels. You may also need to jack up your vehicle, depending on your particular hitch and work space. Read more.
SMALL WELDING JOBS & WELDING REPAIRS
Male in face mask welds with argon-arc welding in the body
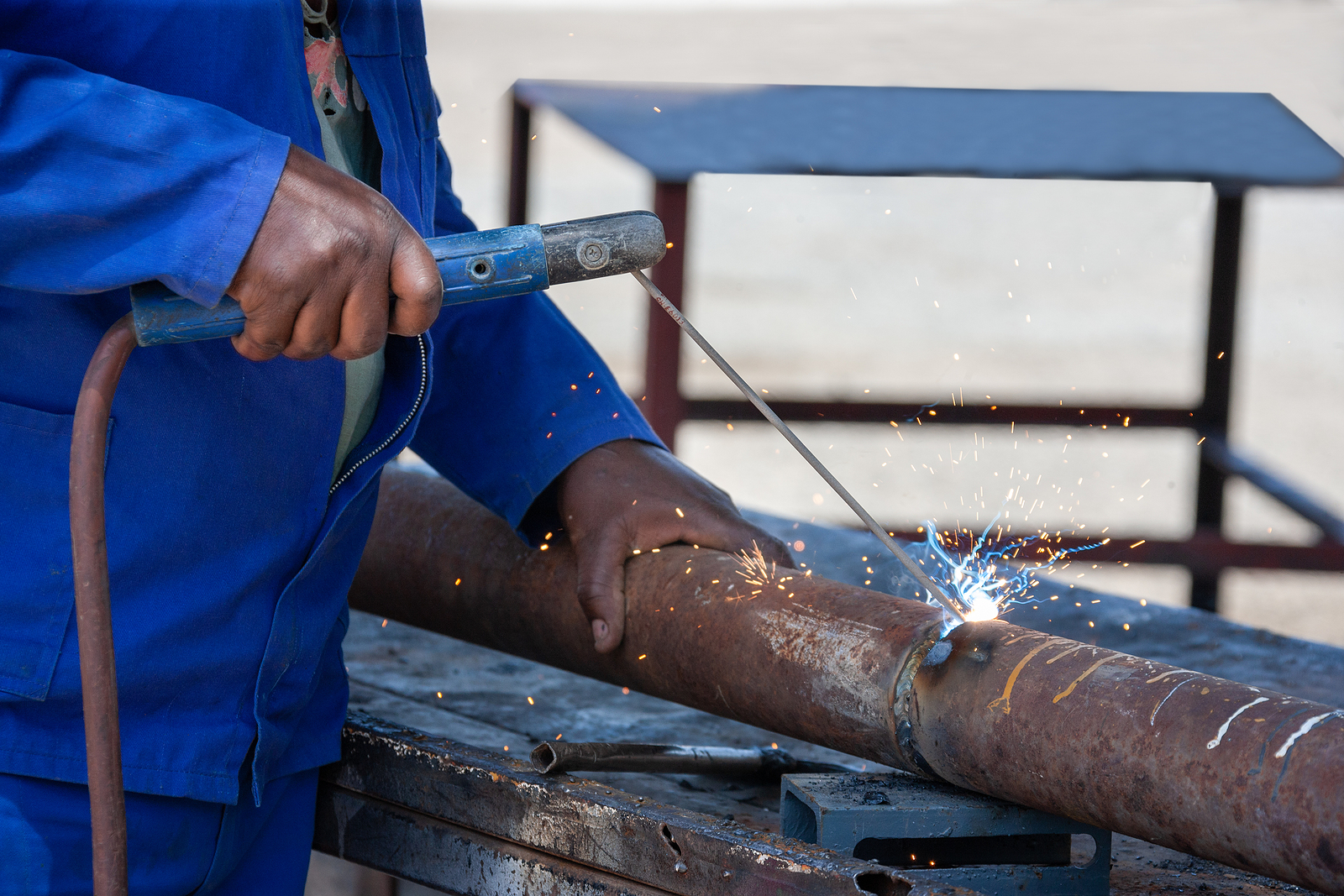
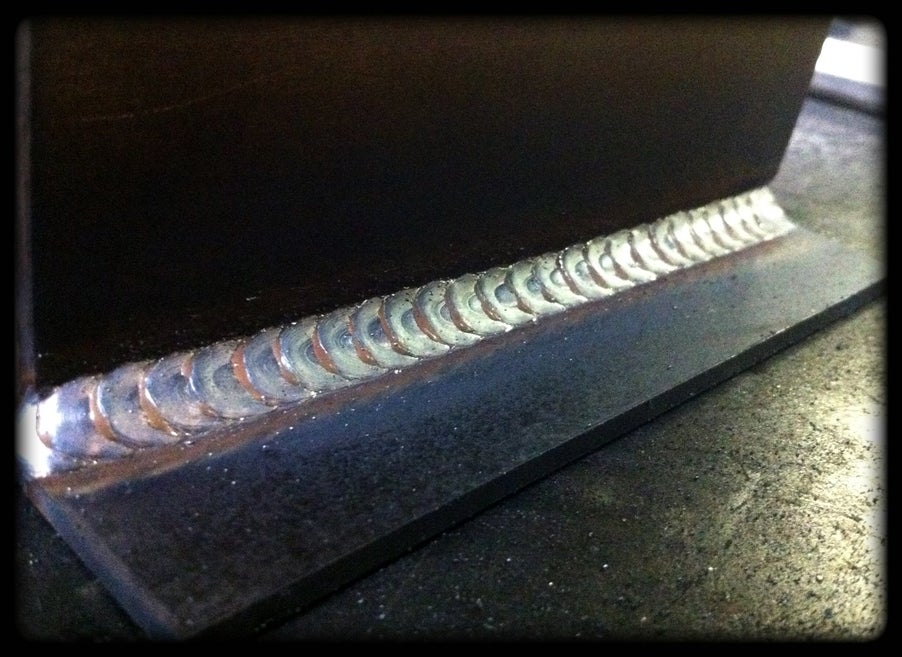
Welding has many applications in the construction industry but the average homeowner can have multiple uses for welding as well. One area welding is used frequently outside of construction is back-yard-mechanics and the Off-Road community. Personally, I weld quite frequently on my 4×4. Everything from fabricating bumpers, shock/motor mounts, roll-cages, and various repairs. So, for our purposes, I am giving directions on how to select equipment, material, fit, tack, and weld plate steel. This can be an especially handy skill when building a custom bumper for your off-road vehicle. So we will demonstrate welding 3/16″-1/4″ plate steel.
Step 1: Equipment: Welder
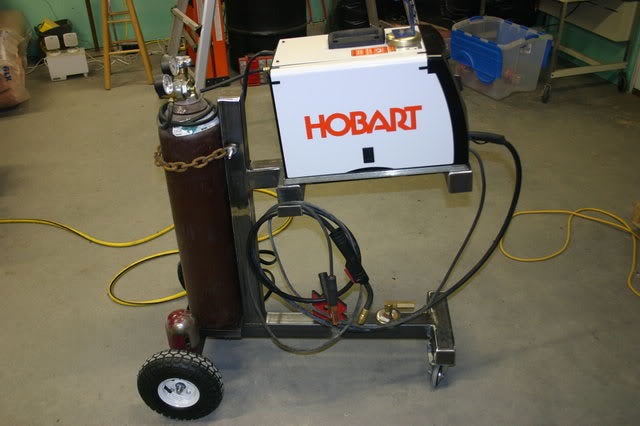
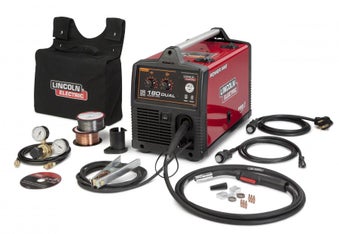
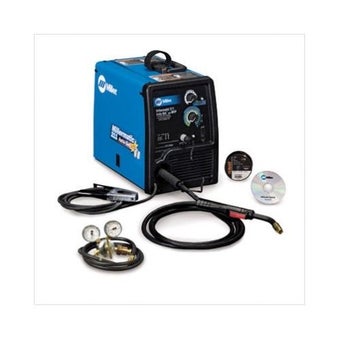
The first thing you need to weld is a welder. There are many different styles and types of welders, but for our purposes we will be focusing on 110volt MIG/GMAW (Metal Inert Gas or Gas Metal Arc Welding). This is most commonly referred to as a “wire-feed” welder. I have selected the 110v because the thickness of material will not exceed 3/8″. There are multiple manufactures of welders, but there are three brands that are top of the field and they are: Lincoln, Miller, and Hobart. The Lincoln brand welders are the most easily accessible in an average home improvement store. If you want a Miller or Hobart you will have to seek out your local welding supply company. This is the route I would suggest as the welders supply will have a better knowledge base and more variety of products. The best tip I can give for anyone selecting a welder is to consider what you will be welding the most and find a welding machine that’s has the appropriate capabilities. One of the most important features is the ability to run solid wire with a shield gas or run a flux core wire. Solid wire uses solid welding wire with a shield gas that comes in a tank that gets hooked up to the welder via a regulator. The flux core wire has the shield gas in the “mixture” of the flux contained within the center of the wire. It is important to note solid wire with a shield gas produces a much cleaner product.
I will be using the Hobart Handler 140 with solid wire and shield gas. The shield gas is a mixture 20% Argon 80% C02. This is a standard mix for mild steel and is available at your local welding supply store.
Cost for the Welder is roughly 500-800 with your shield gas bottle. Read more.
RV CAMPERS HITCH INSTALLATIONS
BONUS BELOW
In this article, we will guide you on how to to the RV Trailer Hitch Installations Step by Step. Preliminary steps to install a trailer hitch are to reconnect the battery which I disconnect usually when I am not going to use the trailer for more than a week so it does not drain. Another preliminary step is to disconnect the hitch lock, that I set up to avoid the travel trailer from being detached and stolen. Likewise, you have to elevate the trailer tongue or trailer nose to be able to position the trailer hitch ball right underneath the coupler.
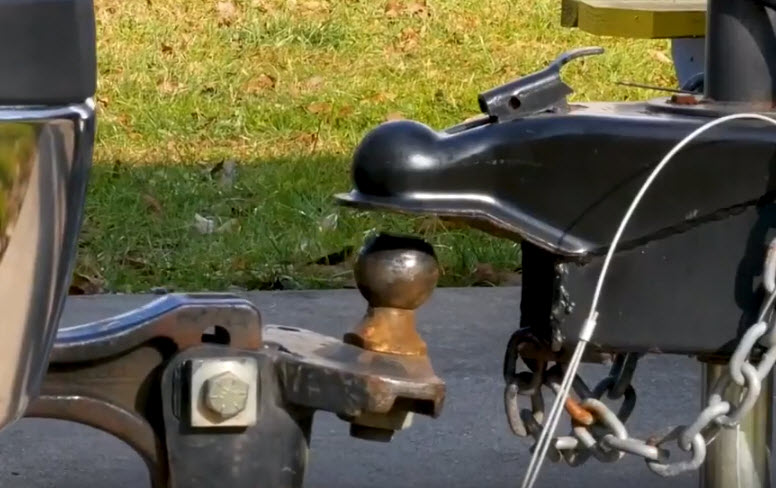
Place the wheel chocks to stabilize the travel trailer in a way that you fix it and will not move. This is a very important step to perform.
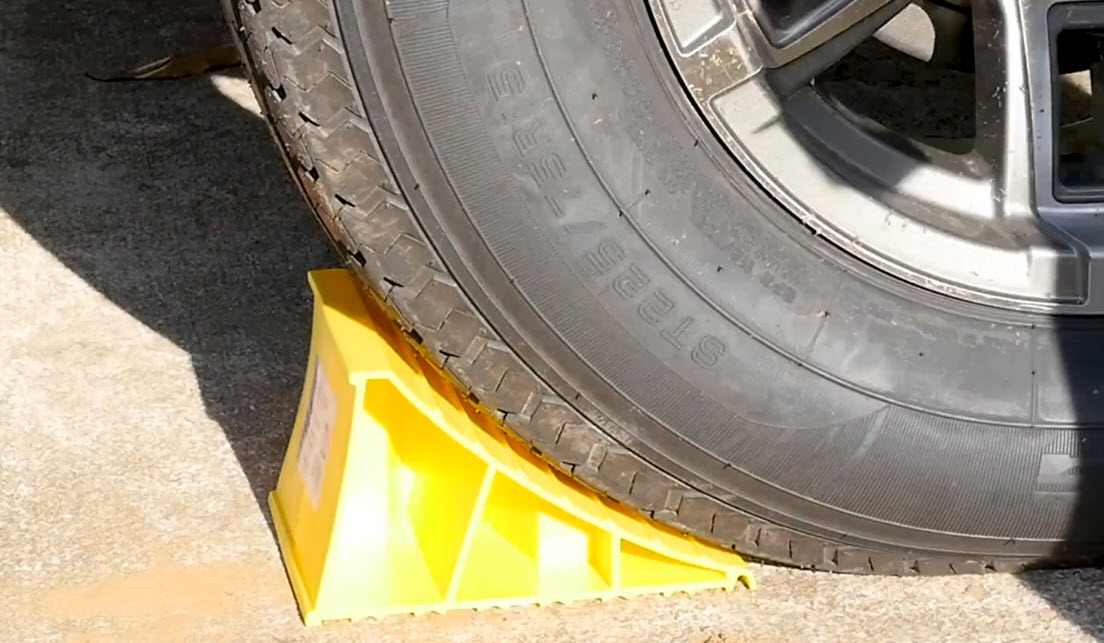
Now proceed to open the coupler latch and utilize the manual or automatic crank to lower the coupler onto the trailer hitch ball.
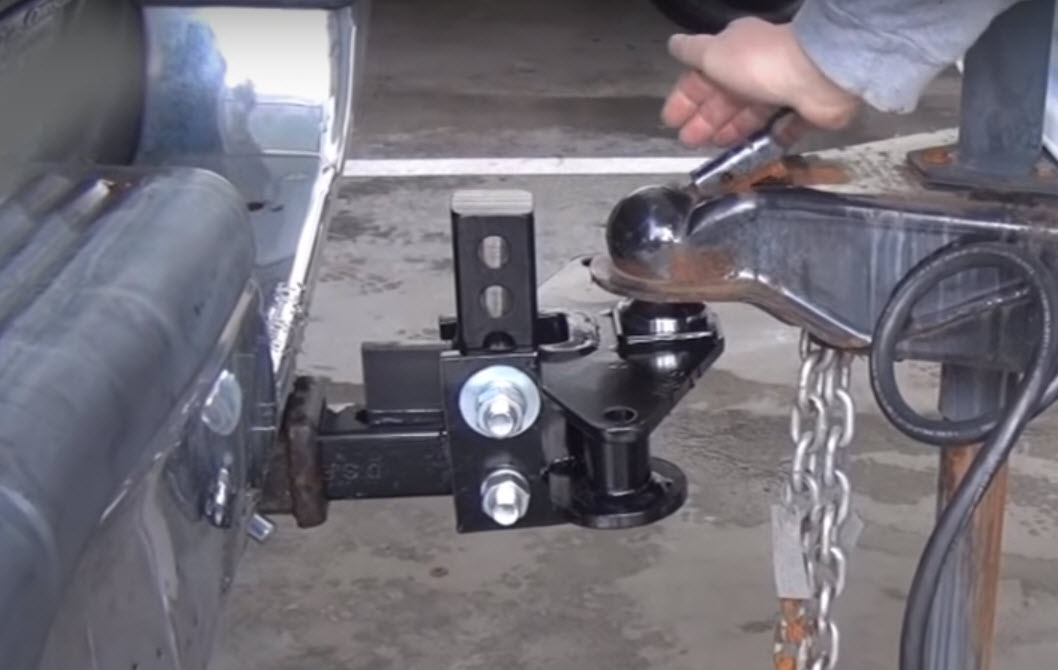
Proceed to the locking of the latch and the next step is the insertion of a hitch pin to prevent the unhitching of the trailer hitch ball afterward. this locking is performed to ensure that the ball is not going to come off of the trailer.
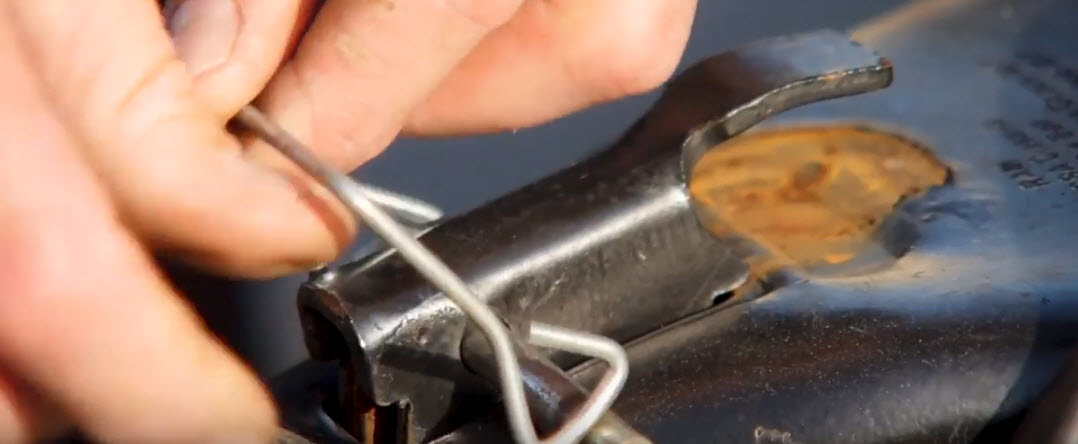
Now after pinning, we will raise the trailer tongue again, as we will continue with the attachments, specifically, the spring bars and other devices to be plugged.
The next step is to attach the trailer hitch pin. Insert the hitch pin from left to right, so it has to be inserted on the left side of the hitch pin receiver tube. This is because the highest place on the highway is the left part. Highways are designed and constructed this way to allow drainage towards the ditches after the rain.
The normal vibrations during the road circulation of the towing vehicle and the travel trailer will drive the trailer hitch pin further inside the receiver, the hitch pin receiver instead of falling out to the road.
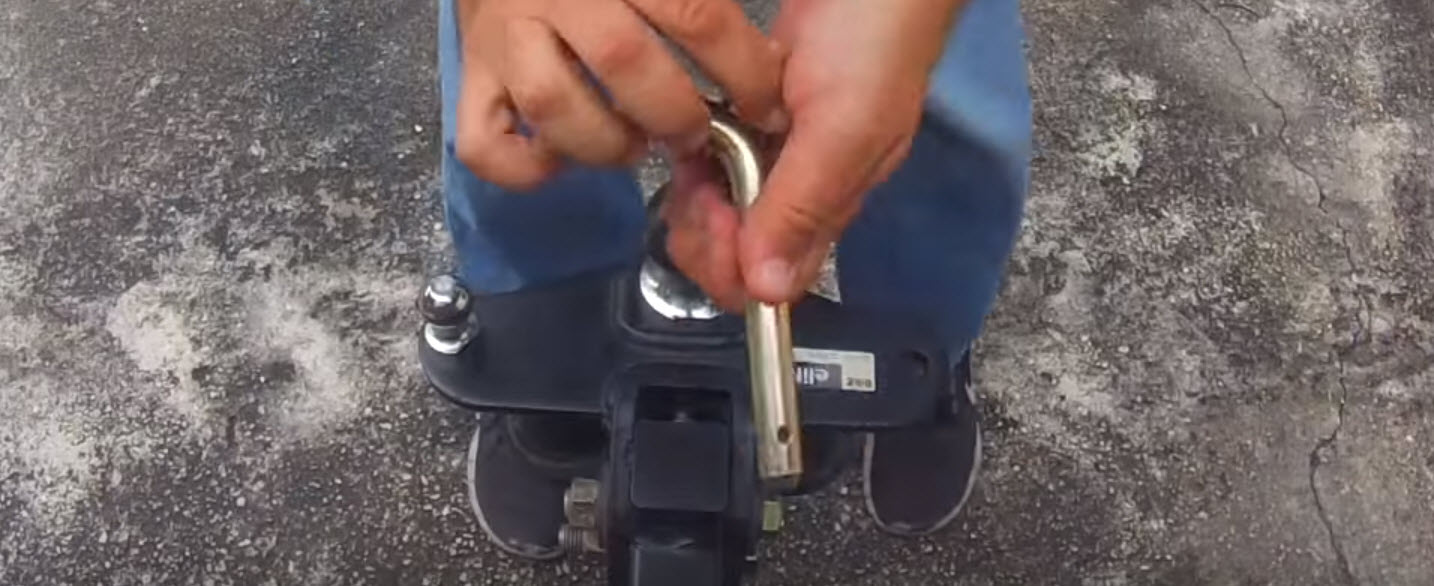
Now, we will hook up our electrical plug. This is a seven-pin connector, so you have light in the travel trailer and your travel trailer brakes will work properly after this connection. This cable should not be dragging in the ground. Read more.
TRAILER WHEEL BEARING REPACK AND LUBE
Don’t have your wheels lock up on you while vacationing with your family or friends.
Don’t risk it for such a small service item.
Of course those with boats dropping in salt water, should be more often.
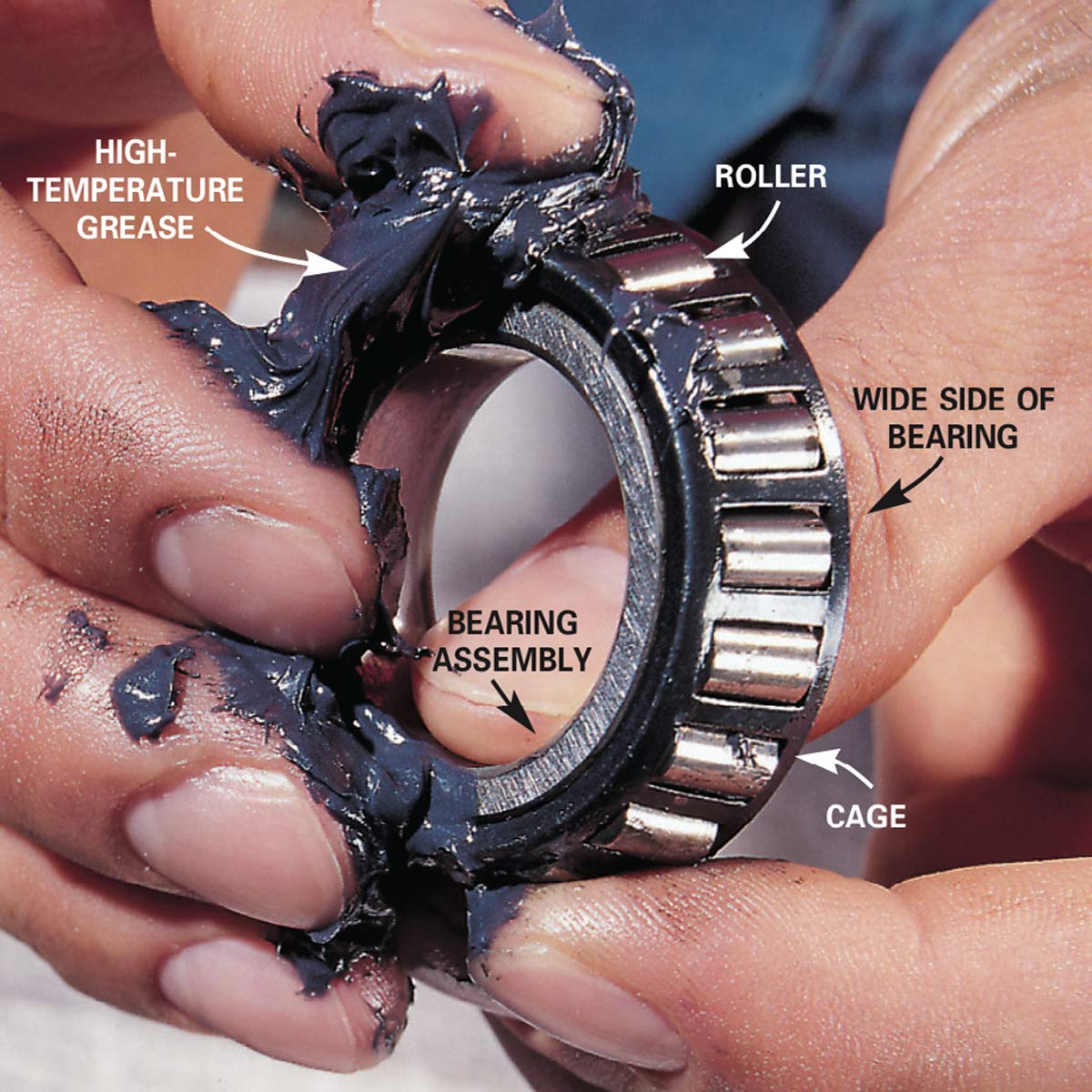
Don’t even think about this Below! Ahh! Don’t get halfway done and find you need a part.
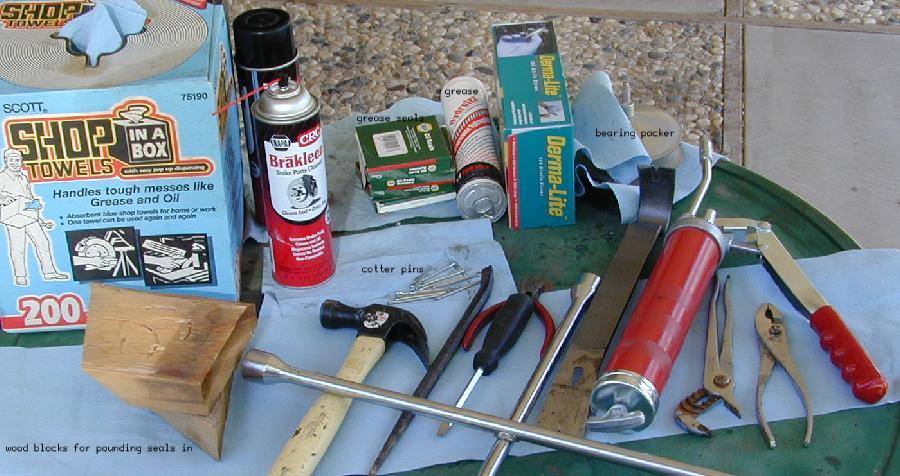
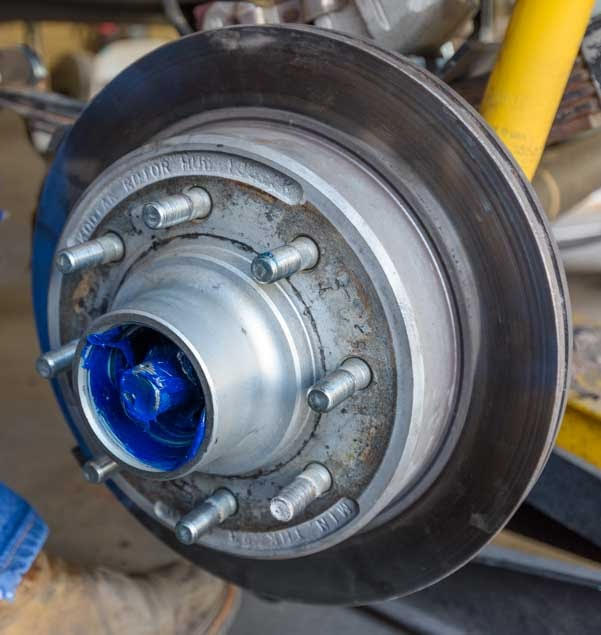
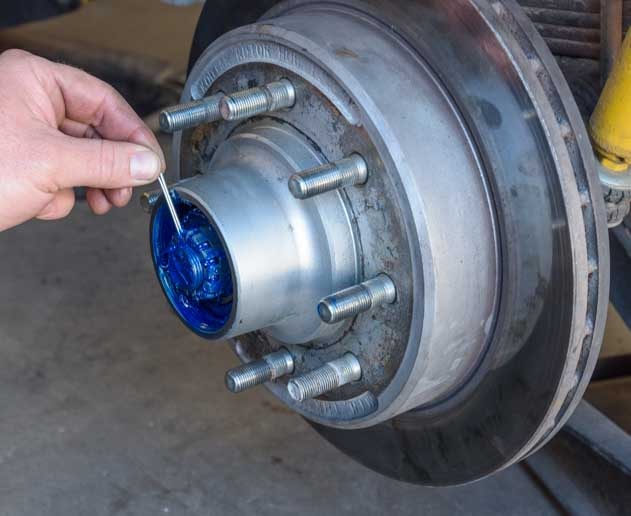
We show you how to repack trailer wheel bearings to prevent the most common trailer breakdown.
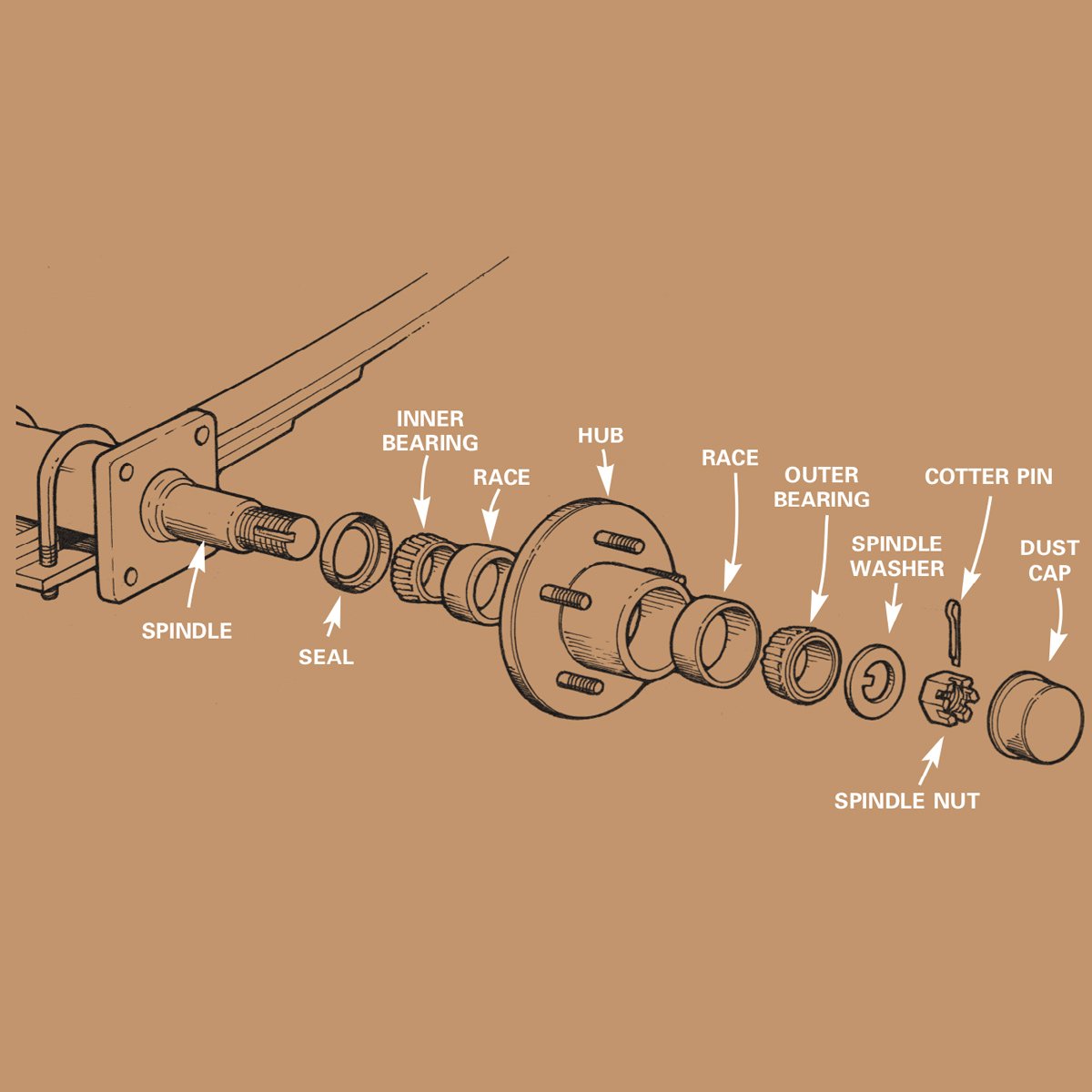
This DIY vehicle maintenance trick is an easy and cheap chore that will save you money in the long run.
Repacking Trailer Wheel Bearings: Step-by-Step Instructions
You know you’re supposed to repack the wheel bearings on your boat, horse, or utility trailer. But do you? Well, not as often as you should, according to Field Editor George Andriotis, who owns D&G Auto and Trailers in Bridgeport, CT. George routinely gets calls from stranded trailer owners. The number one cause? Fried wheel bearings.
You can avoid being stranded by repacking your wheel bearings on a regular schedule. If you use your work or utility trailer daily or drive it long distances, repack them every six months. Repack annually if it gets occasional use and/or the trips are short. For boat trailers, repack the wheel bearings at the start and end of the boating season. Use marine wheel bearing grease.
Repacking wheel bearings is cheap (less than $15) and you can do it yourself in a few hours. Pick up new grease seals, cotter pins, and the wheel bearing grease at any trailer supply shop. Grease seals come in various sizes based on the inside dimension of your wheel bearings. So after you pull off the bearings, take them to the store to match them with new ones. You’ll also need a seal puller, degreaser solution, parts cleaning brush, washing tub, slip-joint pliers, side cutters, floor jack and jack stands. Then follow the simple steps in our maintenance photo series.
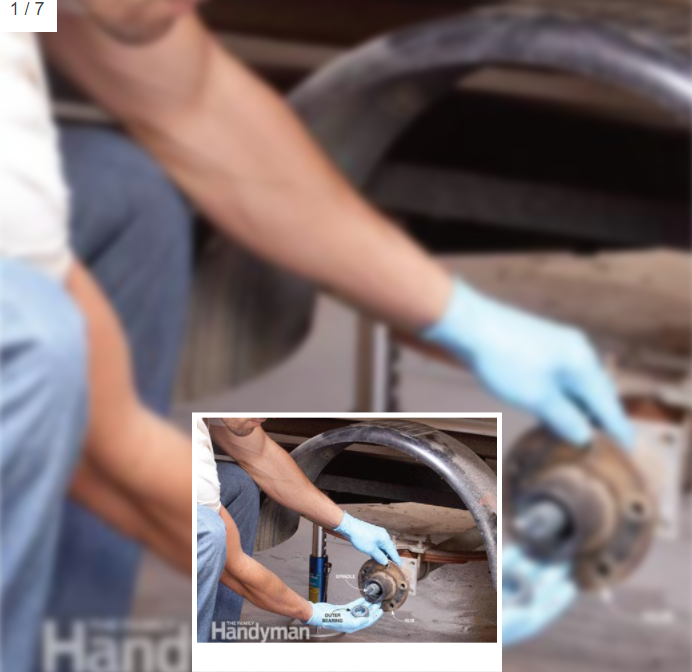
Step 1: Remove the Outer Bearing
Jack up the trailer and support the frame or axles with jack stands. Remove the wheel and then the hub dust cap with slip-joint pliers. Unbend the cotter pin, grab the head with side cutters and leverage it out of the castle nut. Spin the nut off with pliers. Then pull the hub forward until the washer and outer bearing fall into your hand.
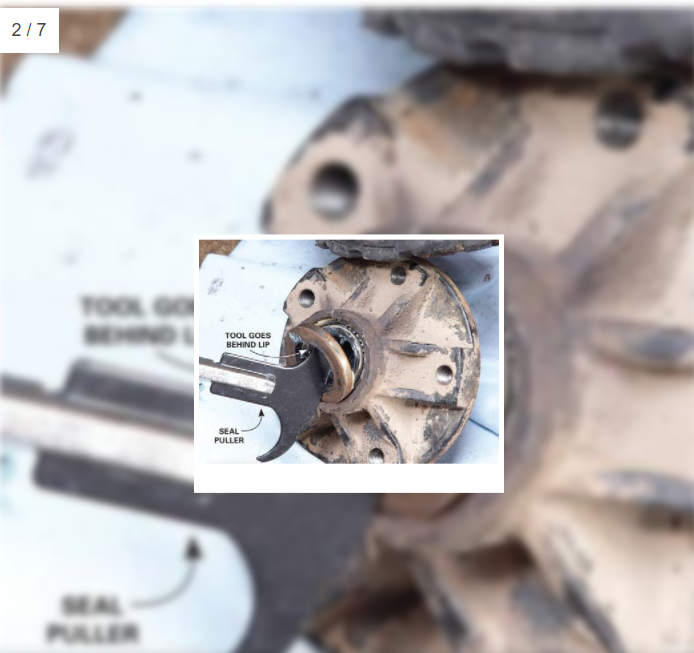
Step 2: Remove the Inner Bearing
Pull the entire hub off the axle and place it on the floor. Hold it with your foot and pry out the grease seal with the seal puller. Keep the inner and outer bearings separate – they have to go back in their original locations. Read more.
We Do Repairs
Repairs
We repair and offer checkups for trailers.
Inspections
For the safety of you and Your Family.
Problem Analysis
Get a thorough understanding of the issues.
Troubleshooting
What is really causing the problem(s).